Air Pollution Control
PENTA SOLUTIONS
Air Pollution Control & Management Systems
PENTA has extensive experience with air pollution control systems and works closely with the Portland Cement Association (PCA) and other relevant industry associations.
The control of pollutants from cement and lime kilns has been a major concern around the world for many years. The Maximum Achievable Control Technology (MACT) requirements and New Source Performance Standards (NSPS) Emission Limits for the cement and lime industries have been the genesis of severe industry changes and will continue to make a significant impact on the cement & lime, mining & metals, minerals processing, frac sand & proppants, and other similar industries going forward.
The cement MACT was issued by the U. S. EPA under the National Emissions Standards for Hazardous Air Pollutants (NESHAP). There are three main types of flue gas desulfurization (FGD) technologies available to assist your facility in achieving SO2 removal equal to or greater than 98%. These are wet scrubbers (or wet FGD), spray dryer absorbers (SDA) and circulating fluid-bed scrubbers also known as circulating dry scrubbers (CDS).
PENTA will analyse your facility for Hazardous Air Pollutants (HAPs), establish (30) day averages, then assist you in remediating any areas that are not in compliance. These include:
- PM 10 and PM 2.5 dust particulates
- NOx
- SO2
- Lead
- Mercury
- Cadmium
- Selenium
- Furan
- Dioxin
EXAMPLE:
PENTA worked on a confidential cement plant in Tejares, NM where the facility was tested and found to be well over the limits for furan and dioxin emissions.
Dioxin and furan emissions are only a problem when heat levels are in a certain range. High heat destroys these emissions, and low heat doesn’t create these emissions in the first place.
CHALLENGES:
- The existing duct work was only slightly angled which allowed dust to accumulate and form dioxin and furan emissions.
- A lack of water in this region to cool facilities.
SOLUTIONS:
- PENTA elevated ducts so they were at a steeper angle which did not allow the dust to accumulate.
- Venting was added to help cool the air/gas in the ducts so the dioxin and furan would not form.
- Water sprays were added to cool the ducts as well, but due to a lack of water in the region, we had to use multiple methods to alter this facility to achieve compliance.
READY TO OPTIMIZE YOUR CEMENT OPERATIONS?
RECENT PROJECTS
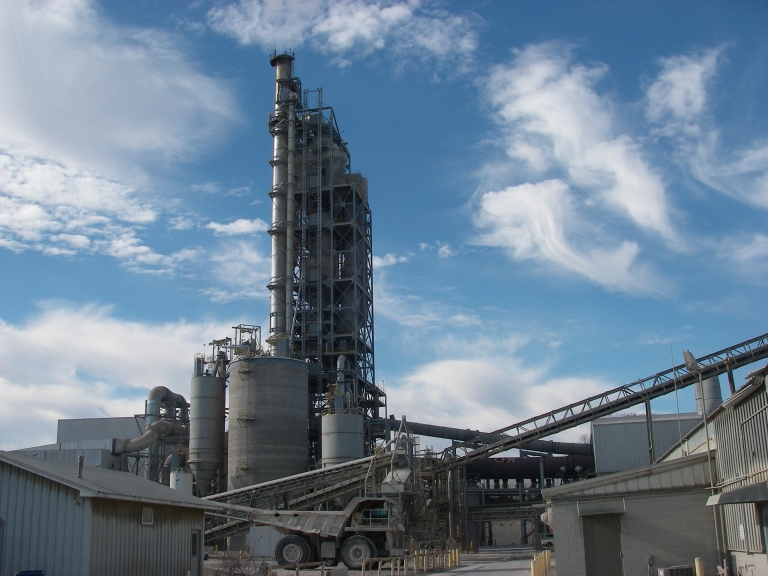
Cement Plant Expansion Structural Engineering
PENTA supported a $500+ Million cement plant modernization project in the Midwestern United States providing structural engineering services to an international equipment supplier.
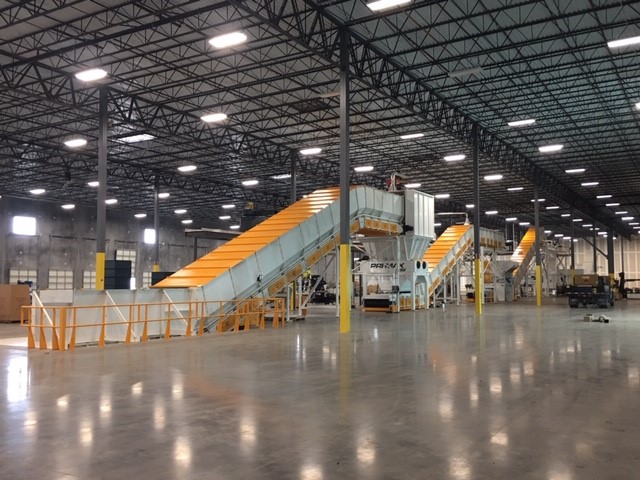
EPCM Waste-To-Fuel Facility
PENTA was engaged to develop a waste-to-fuel production facility that produces a fuel source that can be used in calcination as a substitute for fossil fuels.
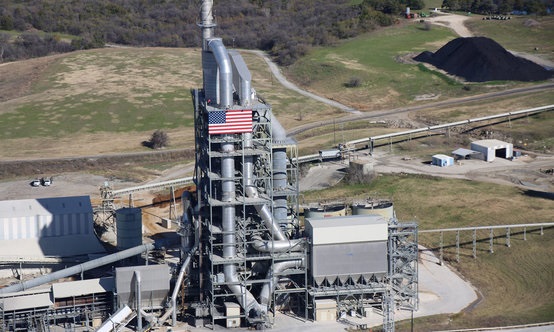
Tire Derived Fuel Facility
PENTA provided the engineering for the installation of a tire derived fuel (TDF) system at a plant in TX.
READY TO
OPTIMIZE
YOUR INDUSTRIAL
OPERATIONS?
Discover how PENTA’s tailored solutions can solve your toughest challenges. Reach out for expert guidance today.