Design/Build Bulk Material Transfer Terminals
PENTA SOLUTIONS
Bulk Materials Handling & Design
LOGISTICS OVERVIEW
Bulk material commodities such as cement, lime, fly ash, slag, and sand need to be distributed to end users as inexpensively and efficiently as possible. The manufacturer’s distribution network consists of:
- Load-out system at the manufacturing operation into a transportation mode (rail, truck, barge, ship)
- Terminals to receive and offload the transportation mode into bulk storage
- Terminal load-out system into a transportation mode to distribute to the end user
Safe, rapid, and environmentally sound transloading of bulk commodity shipments with minimal handling is key to efficient logistics. Two primary concerns to establish efficient logistics are the budget and schedule to build the transfer terminals to meet market opportunities.
LOGISTICS OVERVIEW
- Dry Bulk and Liquid Commodities Storage/Handling
- Transportation Modes – Barge, Ship, Truck, Rail
- Storage Solutions – Flat Storage, Warehouse, Welded Tanks, Bolted Steel Bins, Concrete Silos, Domes
- Pneumatic and Mechanical Conveying Systems
- Modular Systems and Construction
- Integrated Dust Collection/Environmental Systems
COMPLETE PROJECT SOLUTIONS
- Permitting Assistance, Concept Development, Capital Cost Estimation, Schedule Development
- Basic and Detail Engineering (Mechanical, Civil/Structural, Electrical Engineering)
- Procurement of Equipment and Services with inhouse expediting, and field receiving/warehousing management
- Onsite Construction and Safety Management
- Construction (Civil, Mechanical/Erection, Electrical)
- Commissioning (Dry and Wet), Facility Turnover
PROJECT APPROACH
FEASIBILITY STUDIES AND CAPEX
Every project should begin with a feasibility study to evaluate potential terminal sites, storage arrangements, and logistics. Client input for equipment preferences is used as a basis for pricing and design focuses on safe ease of equipment access and serviceability for maintenance and operation. The selection of conveying and transfer equipment and product storage design has significant impact on engineering and procurement cost and schedule. It is also important to select the optimum foundation design with the collaboration of a geotechnical consultant. Once the terminal site is selected and the product storage and material handling equipment defined, a formal design-build project delivery offer is developed. In the design-build approach, a total engineering, equipment supply, construction and facility commissioning package is offered with single point responsibility.
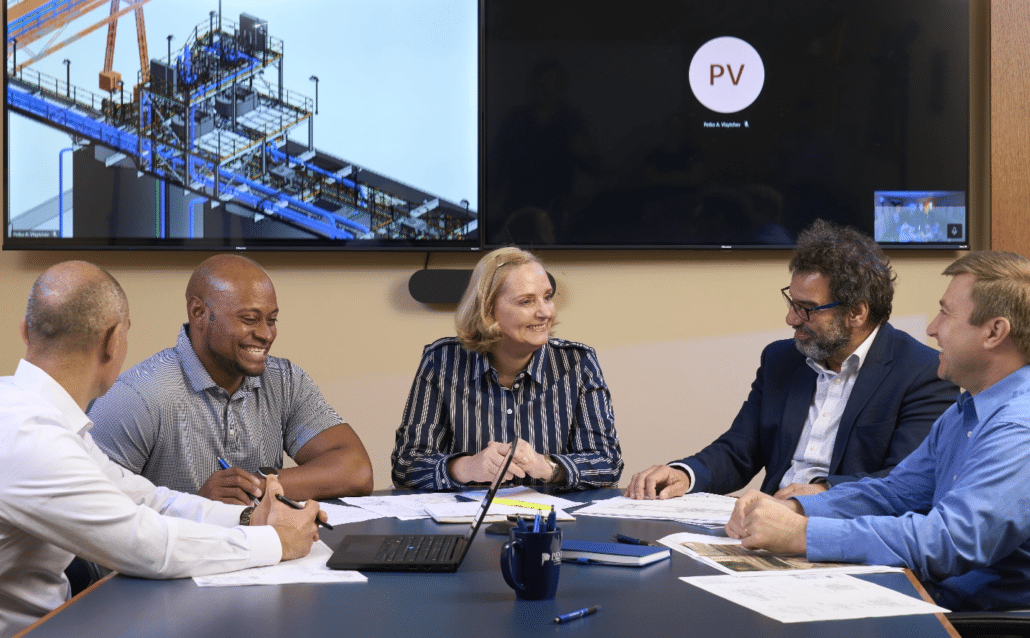
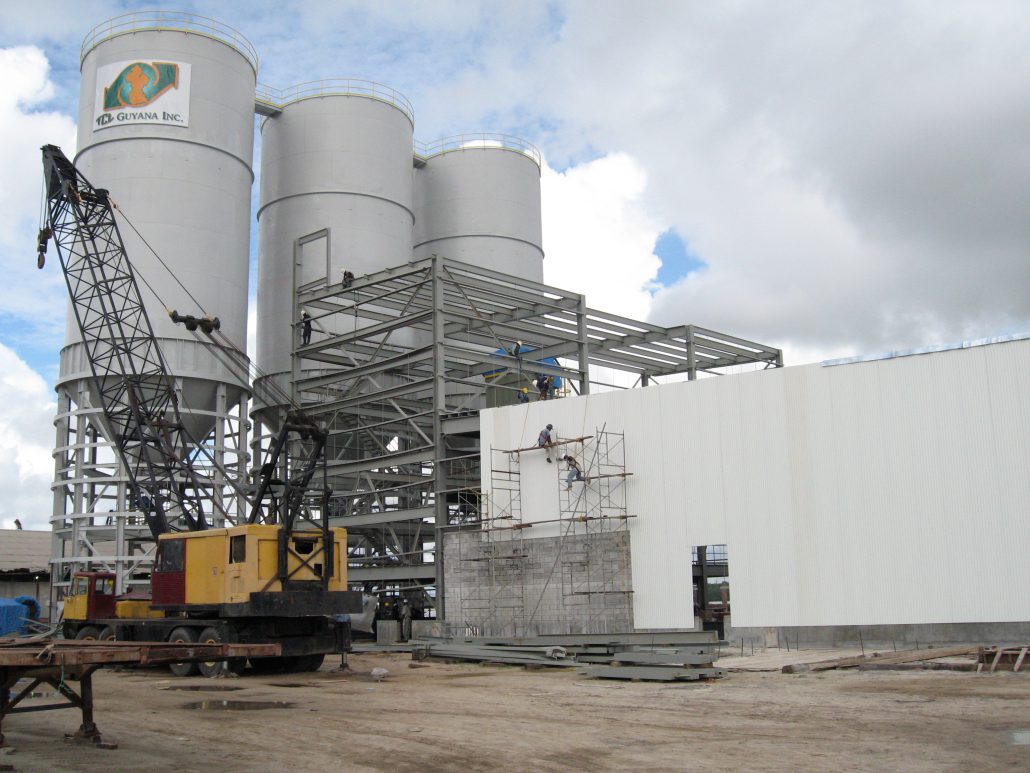
DESIGN-BUILD PROJECT DELIVERY
PENTA takes single point responsibility providing a management team consisting of a Project Manager, Construction Manager and Safety Manager that manages project budget, schedule and safety requirements ensuring successful completion of all project phases. PENTA completes all required engineering (civil/structural, mechanical, and electrical), procurement of all equipment, and completion of construction including site/civil work, mechanical equipment installation, and electrical equipment installation. Modularized systems such as containerized electrical rooms and compressor rooms are utilized to compress construction schedule. Following construction, PENTA manages dry and wet commissioning of the terminal ensuring successful operation before turning over the newly constructed facility to the customer.
CASE STUDIES
Transfer Terminal 1
PENTA recently completed a Greenfield cement distribution terminal in Fort Worth, Texas, on a design/build basis. The client’s planned throughput and the market conditions required a system designed to have two truck load-out spouts under two drive-through steel bins to load two trucks simultaneously. To accommodate maintenance shutdown of one of the silos, the material can be conveyed from either of the silos to both load-out spouts. The terminal consists of PENTA’s proprietary rail unloading system to transfer cement from the railcars to the bins. A rail shed was installed for weather protection. In addition, six-inch blow-off lines are provided to allow cement trucks to unload to either of the silos. Due to stringent regulatory emissions requirements, dust collection was carefully sized and integrated within the system to control emissions. Truck loading was carried out through an aerated bin bottom and dustless loading spouts. The system is fully-automated and the control room is in an office where the operator has a clear view of the loading process through strategically-placed cameras. The office is designed to accommodate the needs of the truck drivers and the terminal operating staff.
Transfer Terminal 2
PENTA was tasked to build a fast-track solution for bulk rail transport and road tanker deliveries in Montana, near the North Dakota border to service the oil fields. PENTA designed, procured and constructed a secondary rail-to-truck loading system while the main terminal was under construction. The secondary system, including rail car unloading, truck loading, truck scale, operator’s station and new rail siding was completed and fully operational within 3.5 months. Power and compressed air supply needs were met with portable systems configured by PENTA. The main terminal consisting of rail car unloading, bulk storage, office/control building and truck loading system was completed within 10 months using extensive prefabrication and modular designs. The secondary system now handles alternate materials and can be used as a backup.
Transfer Terminal 3
PENTA needed to supply a fast-track approach for an owner to receive bulk cement shipments via rail and load customer tanker trucks in Alexandria, Louisiana. PENTA designed, procured and constructed a secondary rail-to-truck loading system while a main terminal was under construction. The secondary system, including new rail siding, main substation, compressor station, rail car unloading, truck loading, truck scale and operators station was completed and fully operational within 4 months. The main cement terminal comprised rail siding modifications, rail car unloading, bulk storage, office/control building and truck loading system and was completed within 6 additional months using extensive prefabrication and modular designs.
READY TO OPTIMIZE YOUR CEMENT OPERATIONS?
RECENT PROJECTS
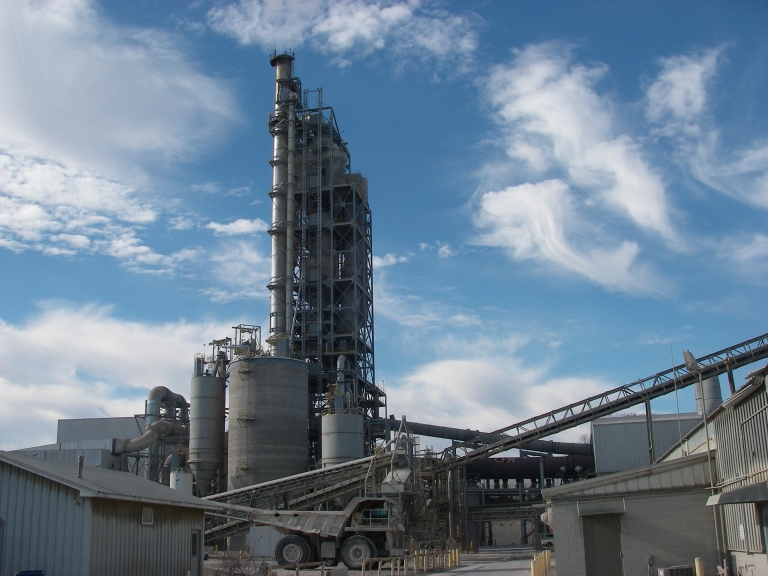
Cement Plant Expansion Structural Engineering
PENTA supported a $500+ Million cement plant modernization project in the Midwestern United States providing structural engineering services to an international equipment supplier.
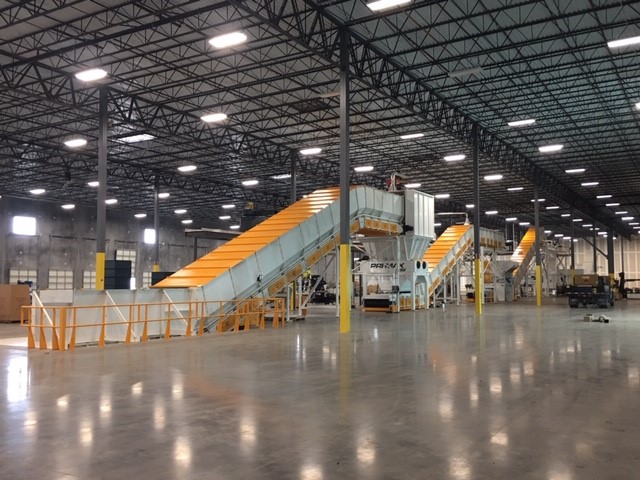
EPCM Waste-To-Fuel Facility
PENTA was engaged to develop a waste-to-fuel production facility that produces a fuel source that can be used in calcination as a substitute for fossil fuels.
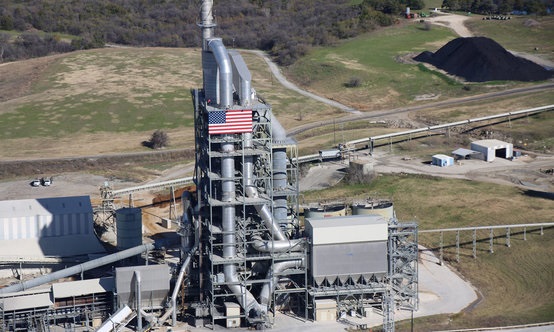
Tire Derived Fuel Facility
PENTA provided the engineering for the installation of a tire derived fuel (TDF) system at a plant in TX.
READY TO
OPTIMIZE
YOUR INDUSTRIAL
OPERATIONS?
Discover how PENTA’s tailored solutions can solve your toughest challenges. Reach out for expert guidance today.